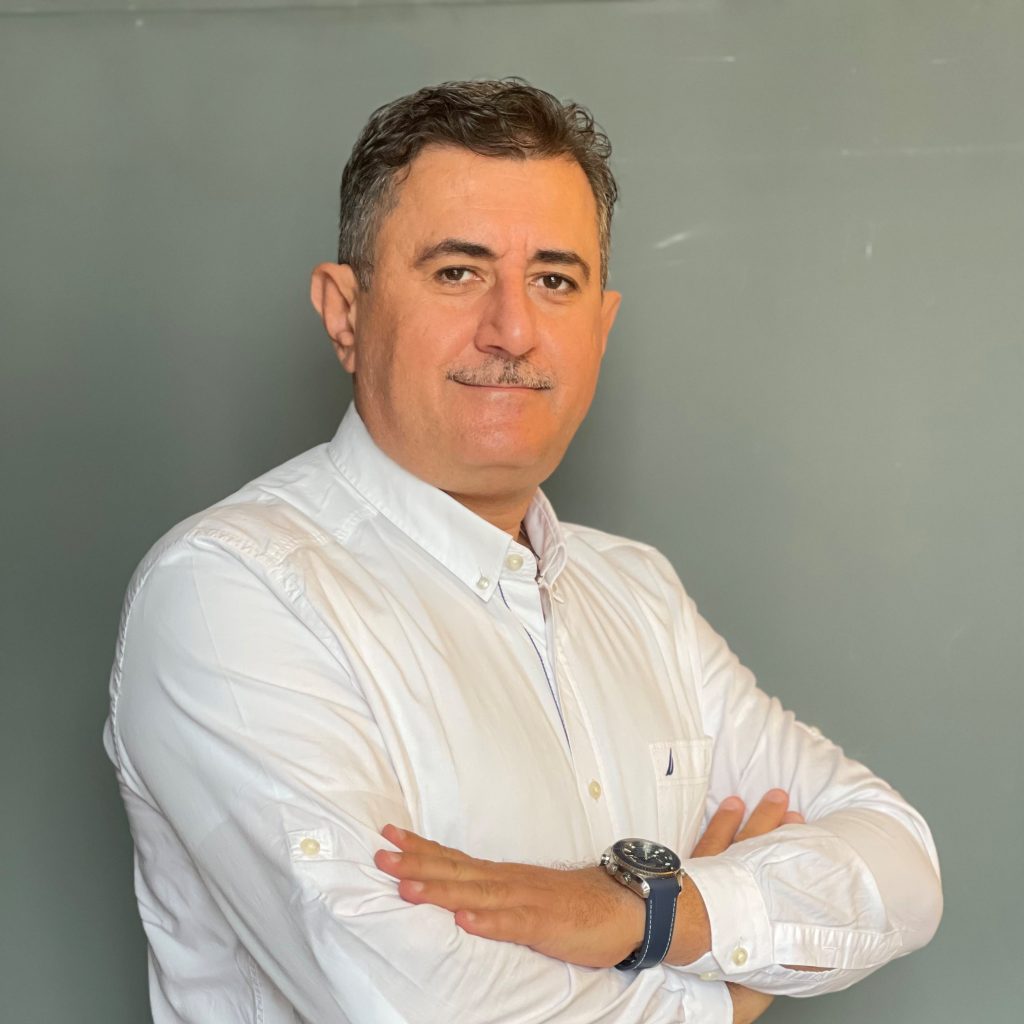
by: Bashar Kayali, General Manager at LINQ Modular
After a decline in 2020, an understandable consequence of the pandemic, the regional construction sector is once again on the upswing. According to the Royal Institution of Chartered Surveyors’ (RICS) Global Construction Monitor Q1 2023 report, the UAE’s construction sector remained “firmly positive” going into 2023, and this is expected to stay the case throughout the year.
In large part, this momentum is being driven by the concurrent boom in the region’s hospitality sector. According to recent projections, the hospitality market in the United Arab Emirates (UAE) is poised for an impressive 25% expansion by 2030. This growth is expected to drive the need for the addition of 48,000 new rooms to the existing stock. In neighbouring Saudi Arabia, the Holy Cities alone are expected to witness the addition of 110,000 units by 2030, in response to the high demand from pilgrims.
Fulfilling this demand will call for an accelerated pace of delivery. While this will no doubt mean plenty of opportunity for construction via traditional means to thrive, the readiness of public and private sector visionaries to embrace cutting edge technologies and techniques means that new methodologies will be presented with the opportunity to cross the chasm from promising concept to proven paradigm. Among these alternatives, few are likely to be as applicable and beneficial to the region’s needs of the hour as modular construction.
Changing Perceptions
With the roots of modern modular construction dating as far back as the 1800s, there has been plenty of room for extensive variation in quality, size, and design of units developed as per this approach. Consequently, this has resulted in some muddied, and arguably less-than-flattering perceptions of modular units (which have largely been utilised for residential purposes). While the application of modular construction for housing developments certainly presents an effective solution to the supply crunch currently witnessed in countries such as the United Kingdom, to focus on this application alone would be to miss the forest for trees.
Indeed, owing to the entry of some of the biggest construction players such as LINQ into the modular construction segment, modular units have come a long way in recent years. So too have the range of applications for which this approach can be feasibly applied. The Dubai Municipality awarding LINQ a licence to pilot the design and build of highly sustainable, customised modular G+6 units mark the first step towards large scale hotels and commercial towers being built in a modular fashion in the Emirate.
The use of top-quality materials, slick designs, and strict adherence to industry best practices have changed both the perception and the possibilities for modular construction.
Modern, in Development and Design
Leading construction players such as LINQ are committed to bringing to market offerings that set the highest benchmarks. As a result, increasingly, modern elements, high quality materials, and even impressive fitouts are being incorporated into modular units. And with today’s advanced fabrication technology now allowing for execution of extremely complex designs, prefabricated units – whether for commercial or residential purposes – have the potential to be as, if not more, affordable than their traditional counterparts. Not just this, they also have the potential to be more aesthetically appealing, and even more sustainable.
Quality and Sustainability
Building operations and construction account for nearly 40% of global energy-related CO2 emissions . With the recent IPCC report highlighting the alarming impact of human greenhouse gas emissions, sustainability is the need of the hour in the construction sector .
By virtue of their design, modular units can be built with a higher percentage of sustainable material than units built from scratch on location. Furthermore, because modular units are produced off-site in purpose-built facilities, there is far more control than at a construction site. Such controlled environments allow for best practices to be stringently followed. Moreover, a high degree of repeatability can be introduced which translates to highly precise processes. All this translates to the potential for better utilisation of resources and less wastage, thereby offering a more sustainable approach.
Timely Delivery
Project delays are all too common in the construction sector — for construction companies this means unnecessary costs and for developers and end-users, a cause of great frustration. This too can be addressed by embracing the modular concept.
The ability of modular construction techniques to effectively mitigate the possibility of project overruns stems from the fact that the factories used to manufacture modular homes are designed around repeatability. Processes can be executed time and time again with laser sharp accuracy, and all the while, data and analytics being applied to uncover potential areas for optimisation. Because skilled labour is utilised at these production facilities, units can be fully fitted out and delivered to their final destinations in ‘near-ready’ conditions. Their installation requires a far lower degree of technical expertise, leading to faster installation on site, with a significantly reduced scope for error. In fact, modular manufacturing is so streamlined that it has been shown to accelerate project timelines by anywhere between 20-50% .
With its modern refresh, modular construction is set to change the construction paradigm, bringing with it benefits through the entire value chain – from construction companies, to developers, community planners and most importantly building occupants. The UK, Singapore, Germany, Sweden, and Japan are all countries where modular construction is an important and well-established part of the industry. It’s only a matter of time before a larger number of nations recognise that the benefits of modular construction are no fabricated truth.